|
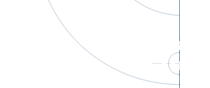 |
 |
An
improperly designed, casually installed, or poorly manufactured gasket
can lead to plant shutdowns, financial losses, plant capacity reductions,
environmental damages and safety hazards that are sometimes fatal.
Therefore there is an increased awareness from customers to enhance
sealing performance. Additionally, there is also a need to understand
the advantages and limitations of newer products such as asbestos
substitutes and other innovative designs. |
 |
WHAT IS A GASKET? |
 |
A
gasket is designed to be placed between two static faces of a flange
in order to affect a seal. The selection of gasket is defined by taking
into consideration factors such as pressure, temperature, and type
of media, etc. The gasket should withstand these parameters in order
to maintain a seal. |
 |
GASKET FUNCTION |
Gasket function can be divided into two stages |
The gasket needs to be properly seated during assembly. In order
to achieve this, the bolt stress should be sufficiently higher
than the internal pressure, hydrostatic end force, and minimum
required bolt stress for gasket seating.
- In a running plant, the gasket needs to maintain resiliency
and recovery properties in order to maintain the same initial
bolt stress and fight against hydrostatic end force and flange
movements due to pressure-temperature fluctuations.
|
 |
|
FACTORS INFLUENCING GASKET FUNCTION |
Many factors can influence gasket function. External factors such
as bolts and flanges should also be considered in conjunction with
gaskets as they influence sealing performance. |
- Application parameters need to be first considered before selecting
a gasket. These include
- Temperature in the system
- Pressure in the system
- Corrosive nature of media
- Viscosity of media
- The following parameters should be considered for gasket selection
- Compression characteristics
- Recovery characteristics
- Chemical resistance
- Stress Retention
- Shouldn't corrode/ damage flanges
- Blow out resistant
- Creep resistant
- Easy to handle
- The above need to be complimented by proper plant maintenance
practices. These include the following
- Flange Condition
- Flange Surface Finish: Different
gaskets require different flange finishes. The flange
finish should be concentric or phonographic and correspond
to the gasket being installed. (Refer to datasheets for
surface finish recommendation)
- Flange Surface Damage: Flange surface
damage can lead to a leakage path, and should be avoided.
- Flange Flatness: An out of flatness
flange or a non parallel flange would lead to uneven compression
on the gasket, and thus effect performance.
- Bolting
- Bolt stress during assembly:
In order to maintain a seal, it is extremely important that
proper bolt stress is maintained during assembly. Proper
bolting equipments should be considered to maintain these
stresses. (Refer to gasket selection for bolt stress information)
- Bolting Procedure: In order to maintain
uniform bolt stress, it is recommended to follow the above
sequence. Bolting should also be done in four stages with
33% torque during the first stage, 66% torque during the
second stage, 100% torque during the third stange, and a
100% retorque during the fourth stage.
- Bolt Lubrication: Good lubrication
is necessary to maintain uniform torque. In the absence
of proper lubrication, torque will be lost to friction.
|
 |
GASKET DESIGN |
Section 8 of the ASME Boiler and Pressure vessel code covers flange
design. It also includes m (gasket factor) and y (minimum gasket seating
stress) values for design purposes. Two conditions need to be considered
separately for gasket design. They are a) Minimum required bolt load
for operating conditions, and b) Minimum required bolt load for gasket
seating. The flange and bolt design should be sufficiently stronger
than these two conditions. This ASME code has certain limitations
as it does not consider certain information such as leakage levels.
Therefore, committees such as PVRC are developing new standards and
constants that would consider design based on maximum permissible
leakage. |
 |
 |
|
Home
:: About Us :: Products
:: Gasket Selection
:: Engineering Info
:: Quality Standards
News :: Contact
Us :: Feedback :: Sitemap |