|
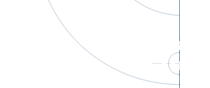 |

|
Starflex presented
a paper on "Productivity and other losses resulting from gasket
problems" at National Seminar on Innovative Strategies in Process
Plant Efficiency Improvement (ISPPEI-2003)held on February 22nd, 2003
by Applied Chemistry Alumni Association (ACAA) of Calcutta University,
Mumbai Chapter. Following are its contents:
|
 |
Productivity and other losses resulting from
gasket problems |
Those in manufacturing sector, especially in chemical industry are
well aware what a poor quality or wrong installation of gasket can
do to plant uptime. An improperly designed, casually installed,
poor quality gasket can lead to plants shutdowns, large sums of
financial losses, reduction in plant capacities and above all cause
considerable environmental damage and pose safety hazards, which
are sometimes fatal.Some of the points, which need our attention
to improve this situation, are discussed bellow.
|
 |
One would find that during a plant turnaround, in most cases gasket
is the only product replaced in a piping system or in the static equipment
being inspected. While a lot of attention is paid to the equipment
inspection but often the attention the gaskets need is missing. From
engineering personnel to operating staff, everyone is concerned about
how fast equipment can be brought back to service and in the process
of urgency, missing a few of the known elements of boxing up flanges.
It may be mentioned that the system is only as strong as its weakest
link, which in many cases is the gasket! |
In most of the organizations standard inspection procedures do not
call for gaskets and flanges inspection. Focus remains primarily on
equipment being inspected leaving a large no of bolted joints un-inspected.
This lack of attention leads to a situation where integrity of flange
joint, practically speaking, is in the hands of maintenance contractor.
Employment of lowest bid contractors may end up in just one leaky
joint to significantly affect the performance of a team. |
A single flange leak delays the testing of the whole piping loop.
There may be a few gaskets like channel to shell gaskets of heat exchangers,
which will be very costly to replace in terms of delay they cause
if, found leaking after box-up. While it is practically difficult
to pay equal attention to all joints, it is worth identifying at least
vital joints at the planning stage.
|
 |
 |
Though the standards specify required quality testing parameters,
there are barely a few who make an effort to ensure that gaskets conform
to standards. Gaskets, considered as consumables, are sometimes ordered
in bulk without adequate attention to quality.
The gaskets, bolts, and flanges are designed such that they can maintain
a higher stress than the internal pressure and hydrostatic end force
in order to maintain a seal. The gasket also needs to maintain recovery
in thickness characteristics to maintain the required stress during
un-torqueing of bolts and flange due to temperature and pressure fluctuations.The
temperature and pressure resistance properties with respect to the
application also need to be ascertained during designA leakage would
occur as a result of mishandling or if any of the above are out of
line.Some of the important quality parameters of gaskets are:
|
-
All gaskets should consistently exhibit compression recovery at
the defined stress in order to maintain a seal.The bolts, and
flanges are designed keeping this in mind. Imagine, in one instance,
a gasket whichis supposed to compress 25% compresses 40% at the
specified stress.During the next use, the same specifications
gasket from the same source compresses 14% at the same specified
torque.
The gasket that compressed 40% instead of
25% would lead us having a load lower than the minimum required
load for operating condition as well as gasket seating.This gasket
would not have the properties to maintain the stress levels for
a long duration and would lead to premature leakage.If it is a
spiral wound gasket, excessive compression stress would put strain
on the outer ring which is harder and would damage the surface
of the flange.
Conversely, the gasket that compressed 14%
instead of 25% would lead us to a require a higher load than the
design load to achieve the require compression.The flange and
bolts are not designed taking this excessive load into consideration.Although
there would be no immediate effects, there would be a slow permanent
damage to the equipment, which would lead to problems such as
bending of the flange, stretching of the bolts, and distortions
on the flange surface.This would also lead to reduced ability
of the equipment to maintain high levels of stresses which would
force reduction in operating pressure within the system to maintain
a seal, and thus may lead to reduced production levels.
Raw material quality is another important factor that can influence
sealing performance.All materials are rated to withstand a particular
temperature and pressure on the assumption that they are supplied
in conformance to the required technical parameters.For example,
following are typical properties for graphite.
Purity |
98% |
Density |
1.0g/cm3
|
Leachable Chloride
ion |
50 ppm |
Leachable Fluoride
ion content |
50 ppm |
Ash Content |
2% |
Temp.Range in
oxidizing atm. |
450 C |
Unfortunately, the demand for lowest prices
leads to compromise on quality of graphite. A compromise in purity
levels, or leachable chloride/ fluoride contents changes the performance
characteristics of the material. Such material would oxidize at
lower temperatures of even 300 C. Additionally, higher chloride/
fluoride content can also contaminate the system specially in
critical applications such as nuclear power plants.
Similarly, there are problems with other gasket
raw materials that can lead to problems. For example if the gasket
is supposed to oil resistance but actually absorbs oil above acceptable
limits and changes in dimensions, one will end up having repeated
leaks.
There are numerous applications that suffer
huge production losses due to constant gasket leakages. In a lot
of such cases, the problem is a result of cheap gasket selection.
|
 |
|
There are a lot of innovative products that can enhance sealing performance
and reduce such problems. PTFE for example suffers extensively from
creep and cold flow. It leads to leakage the moment the flange and
bolts loosen. Unfortunately, PTFE is the best option for acid resistance
and can not be replaced. There are numerous applications where the
plant is forced to shut monthly due to leakage in PTFE gaskets. The
production losses in such cases are huge. Fortunately, there are special
PTFE products which offer very good resistance to creep and cold flow,
and maintain superior stress retention. Although such products are
more expensive, they help improve production through reduced shutdowns,
and thus have replaced all gaskets in such applications in the West.
There are innovative products like cammprofile gaskets, Low stress
gaskets, weld gaskets, flexicarb sheeting materials etc, awareness
of which can definitely help the industry to solve critical gasket
applications. There are products available to take care of gasket
leaks due to gasket porosity, gasket creep and evenvibrations and
hammering in pipelines.
|
 |
|
As we all know in practice, it is very difficult to train all engineering
staff on gasket selection and quality standards and even more to the
workmen who handle them. The best ways to reduce the ‘Leaks’ menace
are:
|
- Understand and spread the knowledge and
importance of gaskets.
- Have flanges inspection and gasket installation
checks as part of turn around inspection procedures [at least
identify and inspect the joints which shall call for longer shutdowns/
are the most unsafe joints when leaking].
- Purchase gaskets with a stricter quality standard
from a manufacturer who can demonstrate conformance to specifications.
- Try innovative products for problem sealing cases.
|
(A properly
selected ‘Quality’ gasket shall definitely payoff in long run.) |
|
 |
 |
|
|
Home
:: About Us :: Products
:: Gasket Selection
:: Engineering Info
:: Quality Standards
News :: Contact
Us :: Feedback :: Sitemap |
|